Welcome to Mechanical
The mechanical subteam is responsible for the design and build of the turbine, with the exception of blades and generator. The main components of the turbine we work on are the blade pitching system, the nacelle, the tower and baseplate, and the foundation.
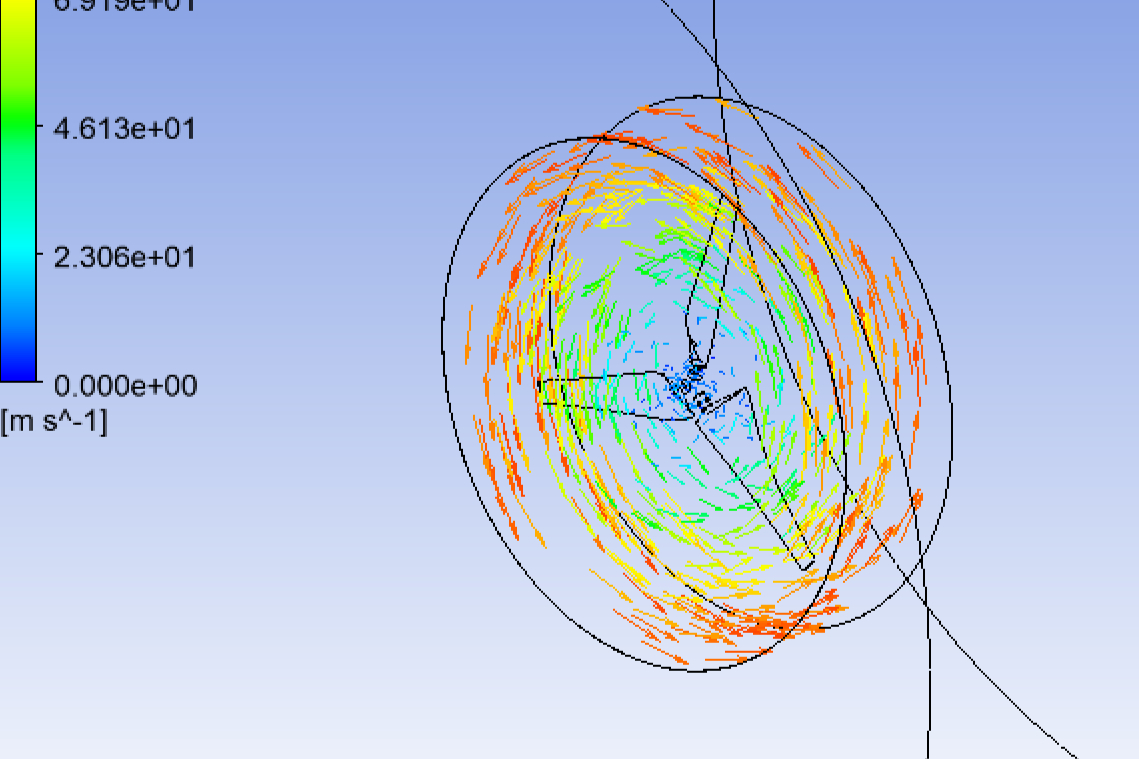
Structures
The structure of the wind turbine includes the tower, the rotor and nacelle assembly, and everything in-between!
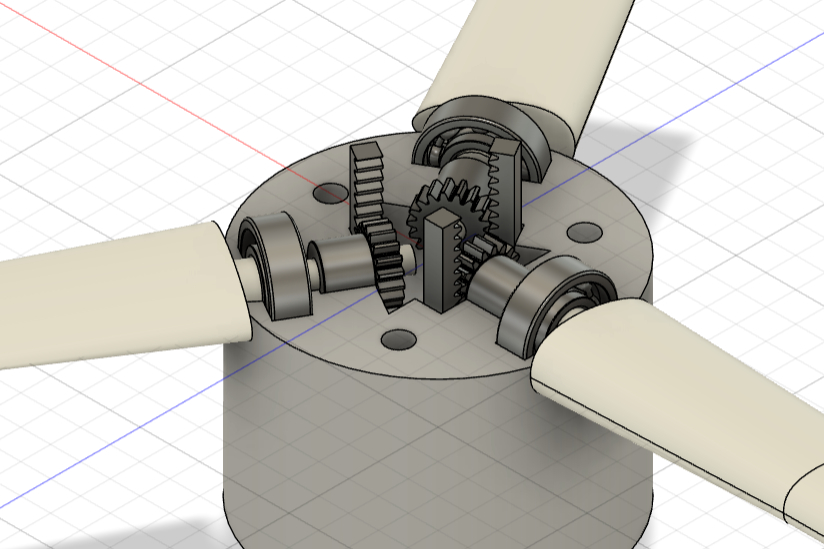
Pitch System
One of the key ways in which we control our turbine, the pitch system adjusts the blades’ angle with respect to the wind.
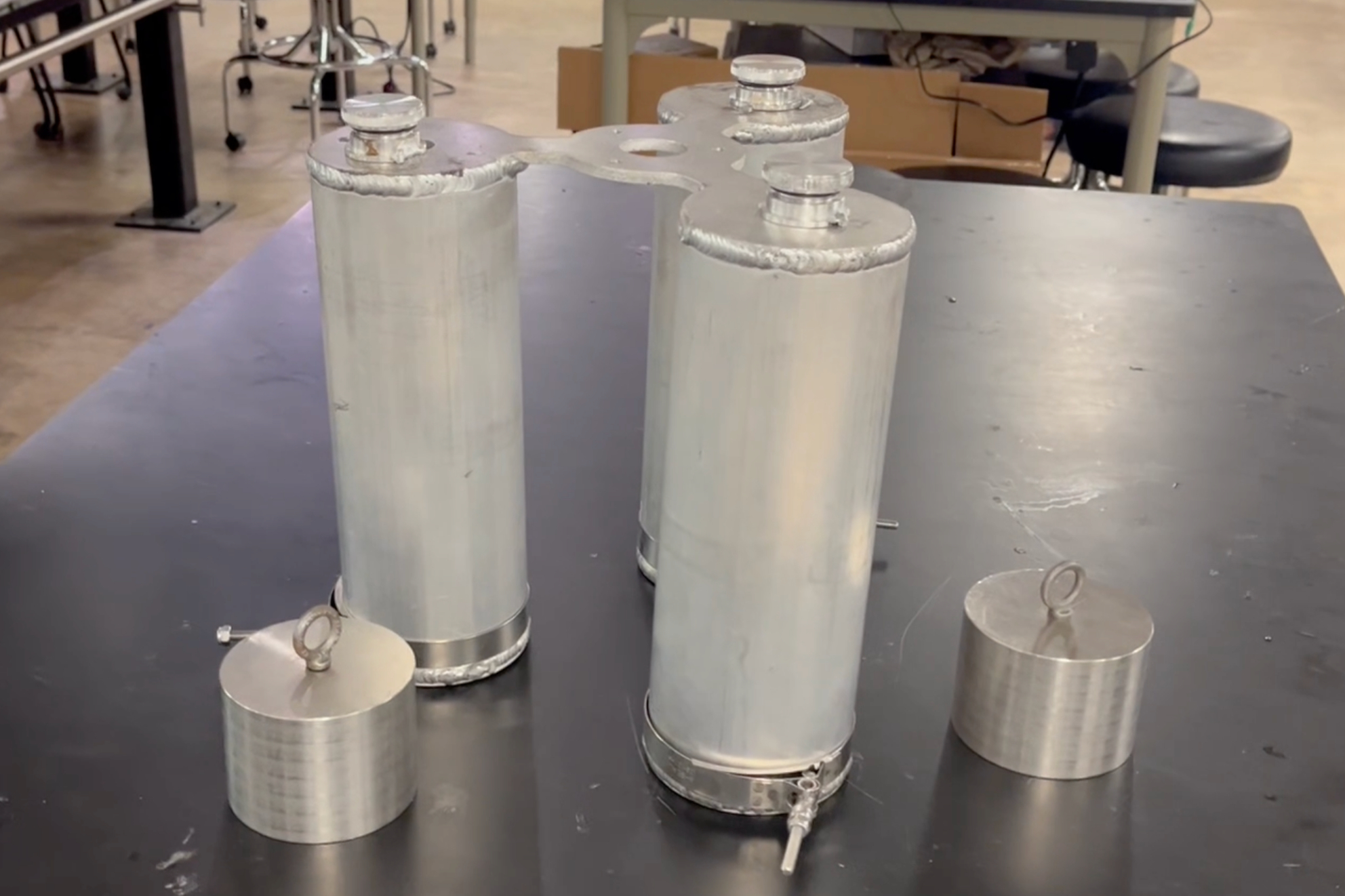
Foundation
Whether it be on land, fixed-bottom on the seabed, or floating on water, every wind turbine must have a robust foundation.
Mechanical
Structures
One of our most important contributions on the Mechanical Team is the structure that supports the rest of the turbine. The structure of our turbine consists of many different components, chief of which include the nacelle, tower, and baseplate.
This year, we are testing an open nacelle design made of a thin aluminum plate, with custom bearing and linear actuator supports. The yaw mechanism will be an aluminum flange bolted to the nacelle plate, secured over the tower with a set screw and a split shaft collar.
To supplement our CAD, we also perform various simulations and calculations to further inform the design of these structural components. This includes simulations for stress and aerodynamics in Ansys, vibrational testing, and much more!
Mechanical
Pitch System
Another one of the key things we build on the Mechanical Team is the turbine’s pitch system. What is a turbine pitch system you ask? By adjusting the angle of the turbine’s blades with respect to the wind, we can effectively control how much torque—and thus mechanical power—is produced by the blades. In the real world, pitch systems play a crucial role in keeping power production steady during normal conditions while also serving to keep the turbine safe if wind speeds get dangerously high.
As for our system, we pitch the blades with a rack and pinion system controlled by a linear actuator at the back of the turbine. We use concentric shafts to integrate with the generator, using the outer shaft to interface with the rotor and the inner shaft to pitch. Through the pitch system, we can adjust the angle of our blades to lower cut-in requirements, improve power generation, or initiate an emergency stop.
Mechanical
Foundation
Although creating the foundation might sound comparatively straightforward compared to other parts of the turbine, things aren’t actually that simple. For starters, depending on where they are located (onshore vs. offshore) wind turbines can have many different types of foundations. In recent years, CWC regulations have been based around offshore wind, where both various fixed-bottom and floating foundation options exist.
In the 2024–2025 competition year, for the first time in competition history, the CWC is based around offshore floating wind. This introduces many new challenges for our turbine design, chief of which include minimizing weight and keeping a lower center of mass. Our design is a 3 column aluminum structure design to have adjustable buoyancy. The foundation connects to four moorings in the bottom of the tank.
Stay Connected
Connect with and follow us on all our networking and social media platforms